Supplier Management is Not Only for Christmas…. David and Goliath
Let’s talk supplier management. Your day-to-day interactions with UK supermarket buyers may feel like going a couple of rounds with a boxing heavyweight. Lots of heavy blows, very one-sided, and little chance of getting anything concrete out of it for you and your business. However, believe it or not, there is usually a quite well thought through and planned strategy. One that they adopt towards you and your competitors in the category. Day-to-day, you see the tactical implementation of that strategy from a buyer who focuses solely on a one-year timeframe to hit budget targets.
Above the buyer will be a category controller and a category director. Their job is to look slightly beyond those rigid (but still oh so vital) budget tramlines to longer-term KPIs. These can be customer engagement, market share and sustainability. And believe it or not, that includes supplier and supply chain sustainability!
In highly brand dominant categories, their supplier management strategy will focus on how to squeeze and play off the various brand players. And how to do this for maximum margin and investment whilst still maintaining adequate shopper choice. For example, soft drinks, soap powder, crisps and snacks and chocolate.
In more own brand dominated categories, the strategy is more orientated around maintaining a sustainable, quality led, and innovative supply base. One that they can still squeeze for margin and investment! For example, ready meals, yoghurts and desserts and cooked meats.
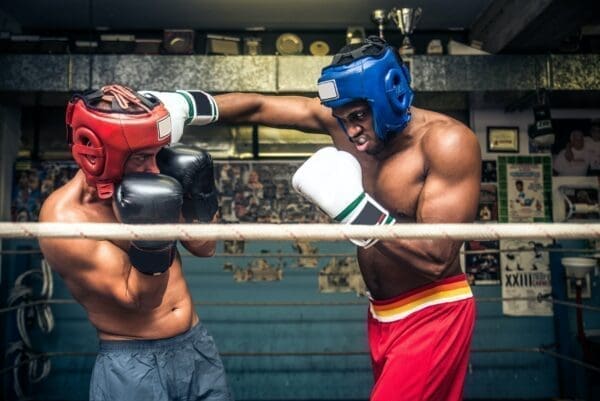
The Supplier Management Account Planning Pyramid
Individual multiple supermarkets will have slightly different models and terminology they use to internally plan their supplier strategies. But a useful ‘catch all’ model is the Account Planning Pyramid. This consists of three layers. With the majority of suppliers managed at the transactional trading terms level rising through the more integrated and structured Joint Business Plan level to the exclusive sunlit upland peak of Strategic Collaboration.
Trading Terms in Supplier Management
At the base trading terms level of strategic supplier management planning the supermarket multiple you supply will have a pretty much purely transactional strategy by which they plan to interact with you. Planning horizons will be pretty short. Regular contact will probably only consist of promotional discussions to their own internal promotional timetable. Annual or bi-annual range reviews plus the inevitable year-end ‘flight-path’ discussions may be the only times you have any meaningful dialogue with them.
From your perspective, you need to ensure that this level of strategic management works as well for you as you can make it. Although you will have very little say in the matter!
GSCOP
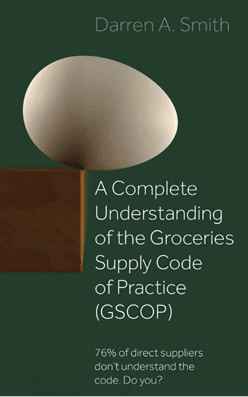
>> Buy on Amazon <<
You have a legal right in 14 of the largest UK grocery multiples to have a GSCOP compliant Written Supply Agreement. It is important that you have one of these as it sets out your legal trading position with the supermarket in question. Also, it offers you (relatively) significant protection from some of the more extreme ways buyers have devised to extract money and investment from you.
Whilst difficult to fully control, you should aim at this level of trading to have a negotiated, balanced structure of the front and back margin delivery of your products for the retailer. Front margin grows directly in line with sales and doesn’t necessarily encourage proactive volume growth delivery from the retailer by itself. Whereas, a well-structured back margin agreement can be relatively cost-effective. Also, it can directly incentivise the retailer to grow your business with them. Furthermore, be aware of ‘back to zero’ growth agreements that reward the retailer. Whatever they decide to do with your order volumes, always aim for a targeted ‘ladder’ structure with clear hurdles. Ones that they have to exceed to get a reward in terms of back margin.
Many suppliers can trade quite successfully with their supermarket customers at this level. It will often suit suppliers whose customer sales portfolio is quite diverse and evenly split. However, on the downside, you may be unable to get traction on your own trade marketing and customer activation plans which could inhibit your opportunities for growth.
A typical supermarket supplier strategy would trade with between 50% and 70% of their supplier base at this trading terms, transactional level, dependent on the category role within their business
Sticky Learning ® is 7 times more effective than 1-day training courses. Plus, you will get a Chain of Evidence proving your Return on Investment. Discover soft skills training that changes behaviours long term.
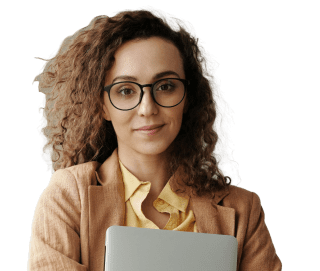
Joint Business Plan (JBP)
The next step up the pyramid is the JBP level. Joint Business Plans come in two very distinct flavours. The genuine ones where the ‘J’ in Joint is respected and forms an integral part of the planning process. Or the false flag JBP where effectively the ‘J’ is replaced by the retailer with an ‘O’ – for ‘Our’ Business Plan.
Buyers often use the vague promise of a Joint Business Plan to tactically position a supplier to extract increased support, investment and margin. These plans have no real ‘J’ in them and need to be seen and treated by suppliers for what they really are – tactical duping by the buyer.
Genuine Joint Business Plans however are something that can help develop and grow your business. They will typical target the classic four ‘P’s of product group marketing – Price (within clear legal constraints), Promotions, Positioning and Product.
Annual Trading Plan
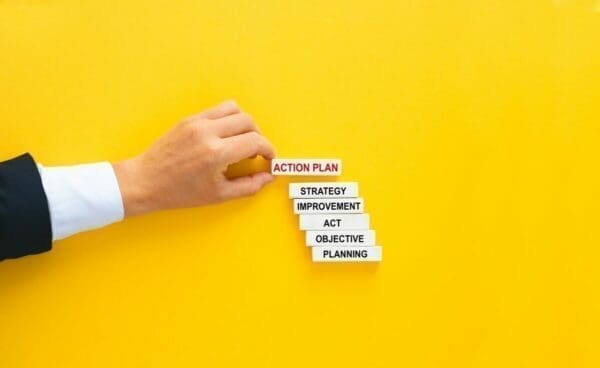
A clear annual trading plan with objectives, targets and timescales for delivery is agreed ahead of the retailer’s financial year. They start with the retailer and supplier regularly reviewing progress, achievement and course correction actions throughout the trading year. There can be clear indicators of whether you truly have a ‘Joint’ Business Plan with them. For example regularity of meetings and proactivity of the buyer in engaging with the plan.
The buyer will negotiate hard to ensure they make the Joint Business Plan work towards the achievement of their annual margin targets. But, you need to equally negotiate forcefully to ensure any margin or investments that are promised are carefully targeted and budgeted to ensure they work for your own trade or business plan. JBP’s can be hugely beneficial for suppliers with a focus on NPD and innovation or with chunky growth targets for their products or brands.
Most buyers, and certainly their superiors, see the huge benefits of having somewhere between 20% and 40% of their category sales volume ‘tied down’ or ‘guaranteed’. With their JBP suppliers tasked with effectively being accountable for a healthy portion of their sales and profit delivery targets.
Strategic Collaboration in Supplier Management
Strategic collaboration is rarely tactically cynically exploited by buyers. At this level, they recognise the long-term strategic value that the supplier brings to the category and/or the wider business. As well as Strategic Partner terms such as Indispensable Business Partner or Strategic Supplier are often used. This represents the very highest level of supplier and retailer engagement. Aside from vertical integration or ownership of a supplying business by the retailer, which is rare in the UK market. Morrisons business model being the notable exception.
Plans are drawn up and jointly agreed usually over at least a two-year time frame if not three to five years. In these times of data-rich shopper insight, the plans usually target long term sustainable shopper activation, engagement and most importantly loyalty metrics.
Collaboration & Integration
Collaboration and integration assume new levels of intensity. The plans will be highly detailed with very clear joint objectives and targets. Cross-functional teams from both retailer and supplier will engage together on specific projects towards to delivery of the joint objectives.
A retailer will have relatively few suppliers at this highest of levels. Mainly because of the time and manpower investment needed to effectively manage this level of relationship. Most Strategic Collaboration suppliers will be ‘cannot do without’ own brand suppliers producing a large proportion of a retailer’s volume in a particular category. Often from retailer specific dedicated factories or plants within factories.

Large scale brand leading suppliers can also (but relatively rarely) feature as part of a retailers’ Strategic Collaboration supplier base. At this level, the retailer will demand specific, bespoke investment in people, products and promotions. This means it becomes a very tricky juggling act for a big brand player with market-wide exposure to pull off successfully.
It is often by the formation of (almost) autonomous retailer-specific business units that such a relationship does succeed. In some cases, integration is taken so far as for the supplier to have ‘implants’ working within the retailer.
Whilst varying by category and in particular by the amount of own-brand products within the category retailers may have between 10% and 20% of their volume dedicated to these collaborative level suppliers.
The ‘Washing Machine’ Spin Cycle
Some retailers are overt in their communication to suppliers as to exactly where they stand in their strategic plans. Most if not, all have models. Usually, a four-box Boston grid brings these to life. Furthermore, different nomenclatures are used. But most terminology usually revolves around Invest/Divest, Grow/Shrink or Engage/Distance.
Indifference
Firstly, the lowest level of ‘spin’ in the cycle of supplier management is ‘Indifference’. The retailer is indifferent to the supplier’s business. Levels of collaboration are low with few contact points with the business. And also, relatively infrequent engagement in meetings or reviews. Friction is also very low, meaning little positive or negative business development discussions about growth, margin or investment. Suppliers stuck in this quadrant are ‘below the radar’ of the buyer. This is sometimes not a bad place to be – especially at a retailer’s year-end!
This quadrant clearly relates to the transactional level of the Account Planning Pyramid.
Maximum Performance
As suppliers grow in size and importance to the retailer, the buyer or the category they outgrow the ability to be placed in the Indifference box and come onto the Buyers ‘radar’. Clearly, the place to be or the place to aim for is the top right-hand quadrant of the model – Maximum Performance.
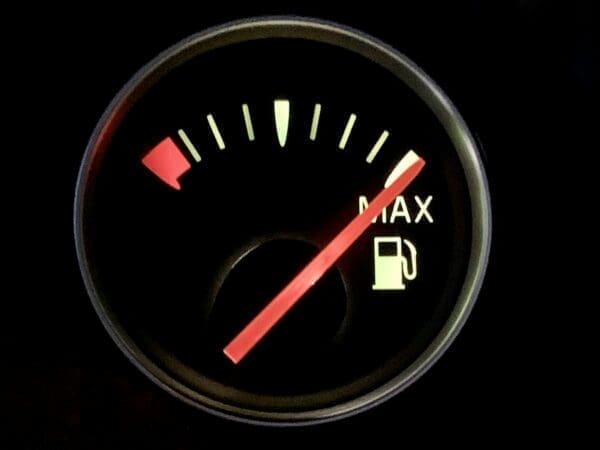
Here levels of Collaboration are very high. The retailer wants to engage with the supplier on many levels and in-depth and across the two respective businesses. Friction is also high. But it is a positive friction that creates positive forward momentum energy that gets things done and targets achieved. This quadrant typically reflects those suppliers with detailed, genuine Joint Business Plans. Or those at the level of Strategic Collaboration
Becalmed
As a supplier, you may aim for and achieve maximum performance. But, with a retailer, nothing always necessarily lasts forever! This is the retailer’s supplier ‘washing machine’ spin cycle in action.
The first signs of you being ‘spun out’ are when levels of friction with the retailer begin to drop off. For example, there is less engagement, less going on, less energy, and urgency from the retailer towards the supplier. Teams frequently cancel or miss scheduled meetings with few or no excuses. Competing suppliers begin to gain traction in the account through new lines, promotional activities, and trade marketing activation. Thus, your business with the retailer starts to stutter and stall. It becomes becalmed – a potentially very dangerous place to be because you may be on your way to Conflict.
Conflict
Conflict takes an aggressive stance instead of a positive and proactive approach. The name suggests that when a buyer believes they can extract more value from a supplier in terms of investment or margin, they adopt a confrontational attitude. As a supplier, you fall out of the top section of the ‘washing machine’ and find yourself in direct conflict.
Levels of Collaboration disappear. They manage you in a highly transactional way. This means levels of friction rocket and ratchet up in a highly negative, confrontational and potentially aggressive way. With outrageous demands and carefully (to stay within the GSCOP law) worded, implied threats.
How the ‘Spin Cycle’ in Supplier Management Works Most Effectively
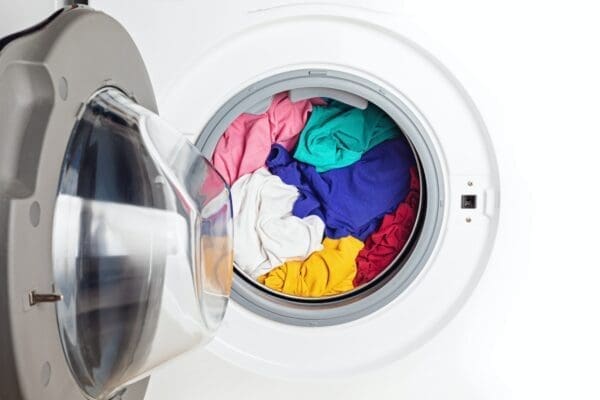
The retailers ‘washing machine’ spin cycle strategy works most effectively in categories with relatively few, large suppliers. Those with brands or product range that shoppers will happily switch and substitute between. Classic categories that retailers employ the ‘spin cycle’ technique on are seasonal confectionery, beer and impulse.
You can actually see the ‘spin cycle’ in action in-store. Look at Easter at which of the big three confectionery brands are stacked up in which retailers front of store. You will quickly see which retailer has which supplier at maximum performance and which is in conflict. Return at Christmas and you will almost always see that the retailers have ‘spun’ the machine. A different branded manufacturer will have the huge front of store stacks of their Christmas confectionary tubs.
Similarly, in beer, look at which of the big four beer brands get prime stack displays during the summer World Cup or European Championships. Then see how the brands ‘spin’ around when it comes to the huge, crucial Christmas trading period
Final Thoughts on Supplier Management
As a supplier, you are not a master of your own destiny. That is when it comes to how you will be managed strategically or tactically by one of the big multiple grocers. Their strategic decisions will determine how they manage you and your business. However, being aware that there is usually a thought through plan, is of huge potential value. A plan that it is possible to move between layers of the pyramid or around the washing machine,
Understand what makes them allocate you to a particular level or box. Then, make plans to either move to a better level or consolidate your preferential position.
Your ability to proactively recognise and plan for how you will be managed will have a direct impact on the success of your business.
Let’s talk Supplier Excellence…
As a Supplier to the Big 4 UK Supermarkets you’ll be challenged regularly to be better. In fact, to achieve Supplier Excellence. Reminded that as a Supplier you’ll need to ‘bring your A game’ and be told that other Suppliers are achieving excellence in certain areas. Therefore your challenge is to ‘raise your game’.
- 2,000 – I have sat on both sides of the fence in this many Supplier meetings.
- 500 – I have worked with this many Suppliers on both sides of the fence.
- £1bn – My last responsibility was for this much sales in one of the big 4 UK Supermarkets.
In that time I have seen Good, Better and Best Suppliers. My intention is to help you achieve the latter – Supplier Excellence.
Getting Through the Door
To be a Supplier we’ll assume that you have great products, low costs, and able to meet the minimum technical, logistical and account management requirements to be a Supplier to one of the big 4 UK Supermarkets.
Don’t Bother Achieving Supplier Excellence?
You could. Many Suppliers achieve a good business as ‘plodders’. Happily telling the Buyers that they ‘don’t do Category Management’, or, ‘They just want to supply xyz and not do all the other stuff. We’re lean’. It is a valid choice. Just bear in mind that as a ‘plodder’, you’re a follower. You cannot expect to receive the first briefing on NPD or be on the inside track; you need to follow the lead set by other suppliers. This is a risky position to be in.
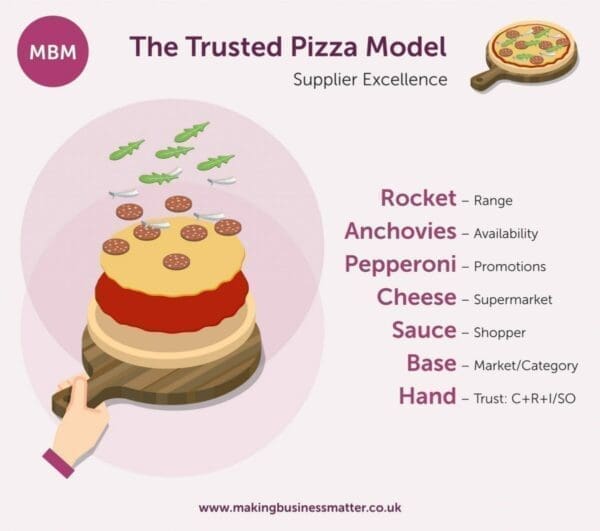
The Mindset of an Excellent Supplier
In short, it’s the 3 legged stool principle. You, the Supplier, working with the Supermarket, and the Shopper, to achieve win:win:win. The 3 legged stool. Yes, the Supermarket may seem to win more and you lose more, but ultimately it is the only model that works.
Stephen Covey, the author of ‘The 7 Habits of highly Effective People’, talks in Habit #4 about win:win. His description challenges the reader in a shop owner scenario that if the shop owner wins, always making decisions that are best for him, he will soon lose his customers. Or if he makes decision just about his customers, he will eventually make a loss and go out of business.

Striving for win:win:win is has to be the mindset because anything else ultimately fails. This mindset must be shared across all functions. It is not the responsibility of just the Commercial Team to solve the Shopper and the Supermarket’s challenges. Every function must understand the what, why, when, which, who, and how of the Shopper if you want to achieve Supplier Excellence.
Action: Identify the Opportunities, e.g. Getting Shoppers to buy more frequently, and share the £xm gap with the team. Then build on this with a one page pen portrait of the Shopper to bring the opportunity to life and get everyone involve thinking like your Shopper.
7 Parts to Achieving Supplier Excellence
Imagine a pizza. Maybe a Goodfella’s deep base, or a Pizza Express Sloppy Giuseppe, or one you’ve made yourself. This will help. We’re going to build one together to understand that there are 7 key parts to achieving Supplier Excellence. Getting these 7 parts right is essential.
1. Base – The Market (Or the Category) – Understand Your Market Better than Anyone Else
To bring this to life in Supplier Excellence terms I ask you to review the latest Shopper research that your business did. The Shopper is likely to say that there is no great difference between the range in one Supermarket versus another.
My example of the ‘whole team mindset’ that is essential to achieving Supplier Excellence, is of a Technical team at a Supplier. They identified that removing the hydrogenated fats from ready meals would provide the point of difference that the Shopper wanted.
2. Sauce – The Shopper – Understand Your Shopper Better than Anyone Else
To bring this to life in Supplier Excellence terms we were working on a Counters project for a Client. The Supplier was concerned about their falling sales on Deli Counters in a Supermarket.
We encouraged one of the production guys to come into store and follow the process of carving and slicing meats in-store. He noticed that the stores were slicing ham at different thicknesses because they do slicing in the factory and he knew about slicing. Sure enough, we went to 10 stores and asked them for 3 slices of Wiltshire ham.
We lined up all the packs and found prices ranging from £1.10 to £1.81. A production team member identified a £xm opportunity that required no additional cost. Shoppers wanted a thicker slice, so each store implemented the change within two weeks by using the same dial setting on their slicer.
3. Cheese – The Supermarket – Understand Your Customer (Supermarket) Better than Anyone Else
To bring this to life in Supplier Excellence terms let’s consider HR. Some HR departments at our Clients have updated their Category Manager descriptions to include a measure on the number of opportunities landed. The industry average percentage of opportunities taken to the Buyer and then successful landed in-store is only 27%. Three quarters are lost. Imagine recruiting and training people on they ability to identify and land opportunities!
4. Rocket – The Range – Understand the Ideal Shopper Range and Better than Anyone Else
To bring this to life in Supplier Excellence terms I want to share a story of bagged salads. Working with this Supplier they wanted to put clear blue water between themselves and their competition. Together we distilled the Shopper research into 5 key decisions that the Shopper makes when they stand in front of the range at the fixture. This helped every person involved in making decisions about the range to know what is important to the Shopper.
Then they dug deeper to understand what each of the decisions really meant. For example, ‘How fresh does this salad look?’. The answer stunned everyone involved in the research and carried through production to offer a fresher salad on the shelf. But it remains a well-kept secret!

5. Anchovies – The Availability – Understand the Where Availability Matters and Does Not Better than Anyone Else
To bring this to life in Supplier Excellence terms please consider frozen foods. Frozen foods have always struggled with space because most of it is taken up by chips and peas. Things that don’t make much money. The packaging team at a Supplier came up with the idea of creating landscape/portrait packs.
On the back was landscape and on the front was the same packaging in portrait. This meant that stores could choose to display the packs either way depending on what freezer cabinets they had. The idea seems obvious now when you think of it, and a great example of internal facing team coming up with a solution to solve an external problem – that’s true Supplier Excellence.
6. Pepperoni – The Promotions – Understand the ROI Better than Anyone Else
To bring this to life in Supplier Excellence terms I let’s talk about the cost of promotions. Of the 500 Suppliers I mentioned at the start only 1 has ever understood how much their spend on promotions and their return on investment.
How about if we knew that we spend £2.5m on promotions and only get back £1.1m? A £1.4m loss. Would Finance be interested to understand and help with that? A typical promotion plan is to promote what you promoted last year. I suggest instead of a drain on cash it could deliver a positive ROI and ideally deliver a benefit for the legged stool, where you, the Supermarket and the Shopper wins. Rather than just switching the Shopper from one product to just a different product in your category.
7. Delivery – The Trust – Having Trust with Your Buyer/Supermarket is Essential to Achieving Supplier Excellence
All of the above cannot happen without trust. Trust consists of five components, which these three articles cover extensively:
-
-
- How to Improve trust with Your Supermarket Buyer
- Not Working Hard Enough to Gain Trust with Your Supermarket Buyer
- Are You Making Mistakes as a Supplier When Selling to the Big 4 UK Supermarkets?
-